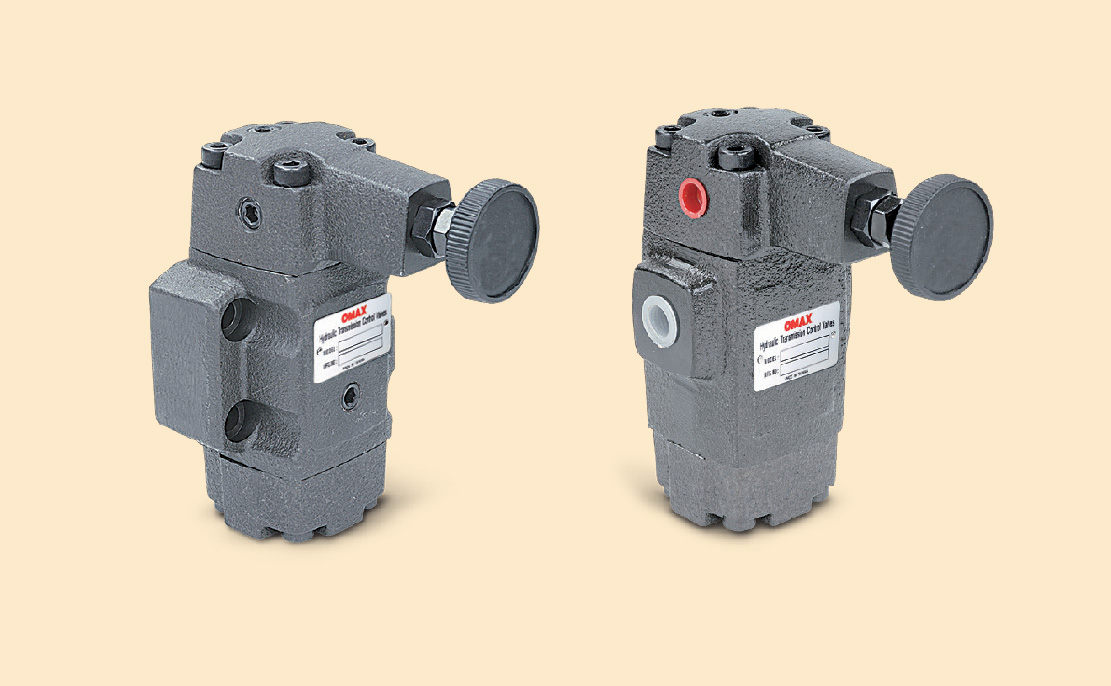
Pressure Reducing Valve
The function of the pressure reducing valve in the pneumatic component system is to reduce the input pressure to the working pressure required by the pneumatic working system and keep the pressure constant, which can control the branch circuit to obtain a stable pressure lower than the main circuit oil pressure.
There are two types of pressure regulators, direct-acting and pilot-operated.
* Direct acting type is the use of spring force to achieve the purpose of regulating pressure.
* The pilot-operated type uses a pre-adjusted air pressure instead of a direct-acting pressure-regulating spring to achieve the purpose of pressure regulation.
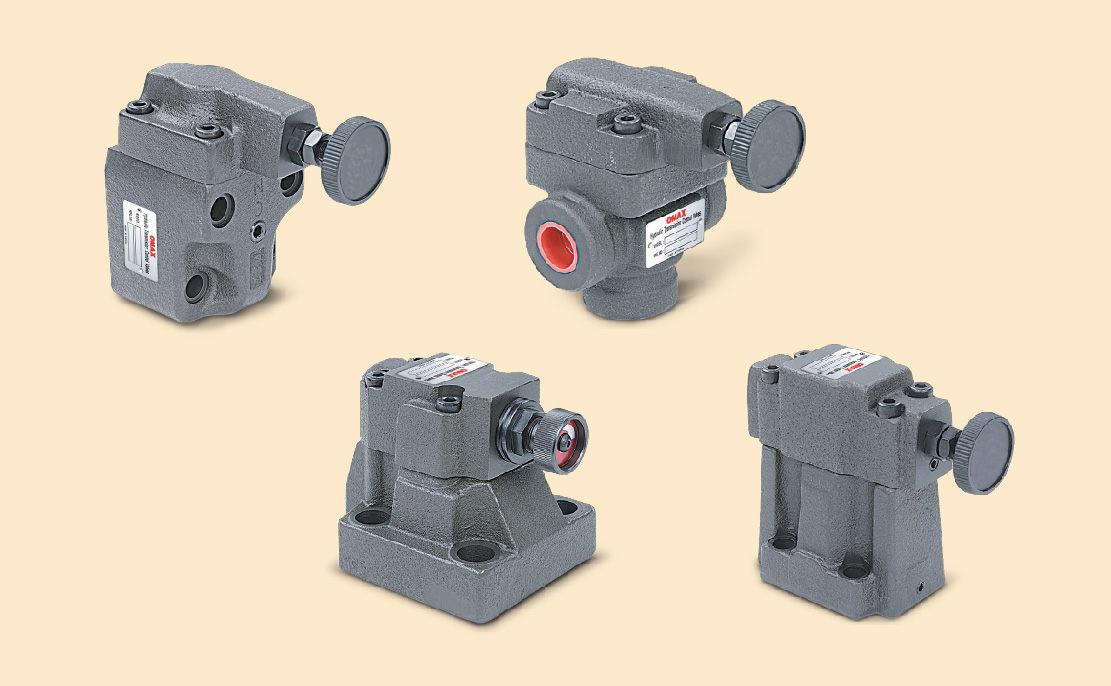
Relief Valve
The role of the relief valve in the pneumatic component system is to exhaust excess compressed air when the operating pressure in the system exceeds a set value to ensure that the inlet pressure is set. Relief valves that act as safety protection (overload) in the system are called safety valves.
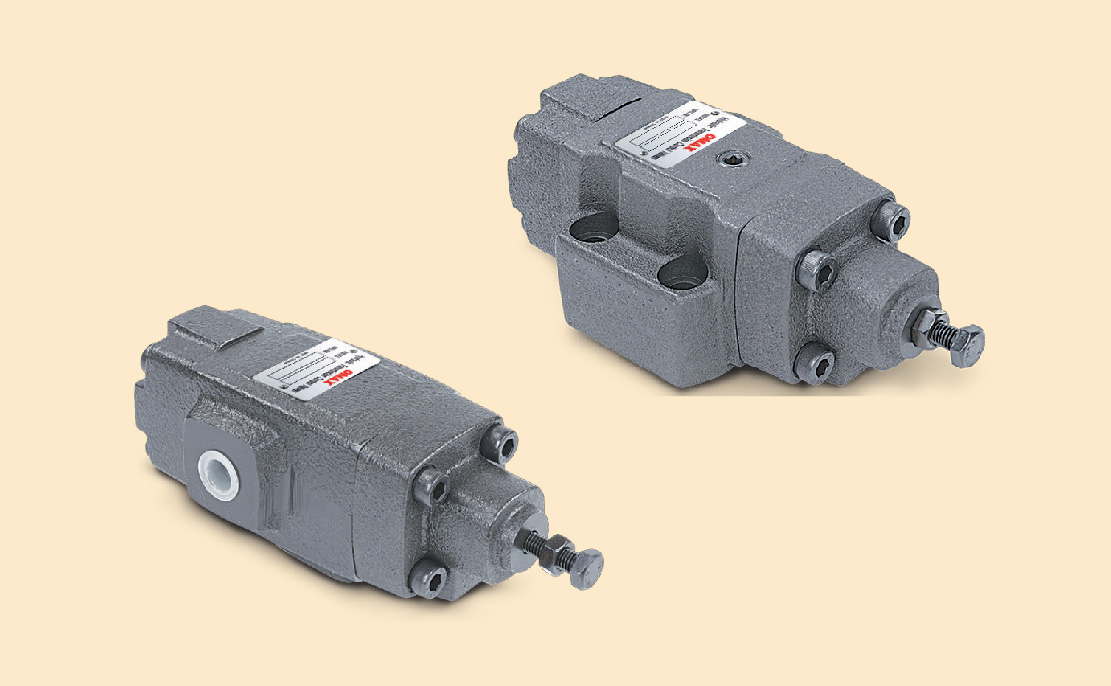
Sequence Valve
The sequence valve is a pressure control valve that uses the pressure change in the circuit to control the sequence of actions. After an actuator (such as a hydraulic cylinder, a hydraulic motor, etc.) can be operated, other actuators can be operated in sequence.
The pressure generated by the oil pump first pushes the hydraulic cylinder 1 to move. At the same time, the oil inlet of the sequence valve acts on the area A. When the hydraulic cylinder 1 moves completely, the pressure increases, and the upward thrust acting on the area A is greater than the setting of the spring. After the value, the valve core rises so that the oil inlet and the oil outlet communicate and the hydraulic cylinder 2 moves.
Valve Structure
1
Adjusting Screw
2
Body
3
Pressure Regulating Spring
4
Bias Disk
An annular groove is formed on the deflector plate to change the flow direction of the oil outlet of the poppet valve. The deflector disk is then subjected to a hydraulic force which is in the opposite direction of the spring force and increases with the increase of the overflow. As the overflow increases, the spring force increases due to the increased opening of the poppet. However, because the hydrodynamic forces also increase at the same time, the structure counteracts the increment of the spring force. Therefore, the inlet pressure of this kind of valve is not affected by the change of flow rate, its p-Q characteristic curve is ideal, the opening and closing characteristic is good, and it is beneficial to increase the rated flow of the valve.
5
Cone Valve
6
Damping Piston
Function One: It is the damping effect when the cone valve is opened or closed, which is used to improve the pressure regulation stability of the valve.
Function Two: It is to guide the cone valve to improve the sealing performance of the valve.
1. Safety valve action (preventing overloading of the hydraulic system). The relief valve acts as a safety valve in order to limit the maximum pressure of the hydraulic system to ensure the safety of the system. Under normal operating conditions of the system, the valve is closed without overflow, and the working pressure of the system is determined by the external load. When the system pressure reaches the set pressure of the valve, the valve opens to overflow. At this time, the system pressure is determined by the set pressure of the relief valve.
2. Relief valve action (maintaining hydraulic system pressure constant): In the throttle control system, the relief valve is normally open during normal operation and the excess hydraulic fluid is drained back to the tank to maintain a constant hydraulic system pressure.
3. With the hydraulic system unloading the remote control port of the pilot relief valve, the relief valve can be used to unload the system. "DBW Low Noise Type Solenoid Pilot Operated Relief Valve" can use its own electromagnetic directional valve to realize system unloading. For other pilot relief valve to realize system unloading, it is necessary to add directional valve to the remote control port.
4. Remote pressure regulation The remote pressure control valve on the remote control port of the pilot relief valve can realize remote pressure regulation.
* The relief valve can also be used as a back pressure valve to make the system work smoothly.
* The relief valve cooperates with the solenoid operated directional control valve to realize multi-stage pressure control of the system.
* In the brake circuit, the brake action can be achieved with an overflow valve.
* In the hydraulic test bench system, the overflow valve can be used as a load valve.
1. Solenoid valve does not work after power on → And re-wiring connector is connected to the power supply voltage is checked in the ± of operating range → Adjust the normal position of the coil → Reweld coil short circuit → Replace coil working pressure difference is not appropriate → Adjust pressure difference → Or replace the appropriate solenoid valve fluid temperature is too high → Replacing the electromagnetic valve with impurities causes the main valve core and moving iron core of the electromagnetic valve to get stuck → For cleaning, if the seal is damaged, the seal should be replaced and the filter installed. The viscosity of the liquid is too high, the frequency is too high and the service life is reached → Replace the product.
2. The solenoid valve cannot close the main spool or the iron core seal is damaged → Replace the seal fluid temperature, viscosity is too high → Replace the solenoid valve of the counterpart with impurities into the solenoid valve core or moving core → Cleaning spring has reached or deformed → Replacement of orifice balance hole plugged → Timely cleaning work frequency is too high or life is reached → Reselect products or update products.
3. Leak in other situations → Check if the seal is damaged or the spring is not fit. → Loose connection or seal is bad → There is noise when tightening the screw or replacing the seal → The solid pieces on the head are loosened and tightened. The voltage fluctuation is not within the permissible range and the voltage is adjusted. Core suction surface impurities or uneven, timely cleaning or replacement.